Understanding the Power of Materialise in 3D Printing
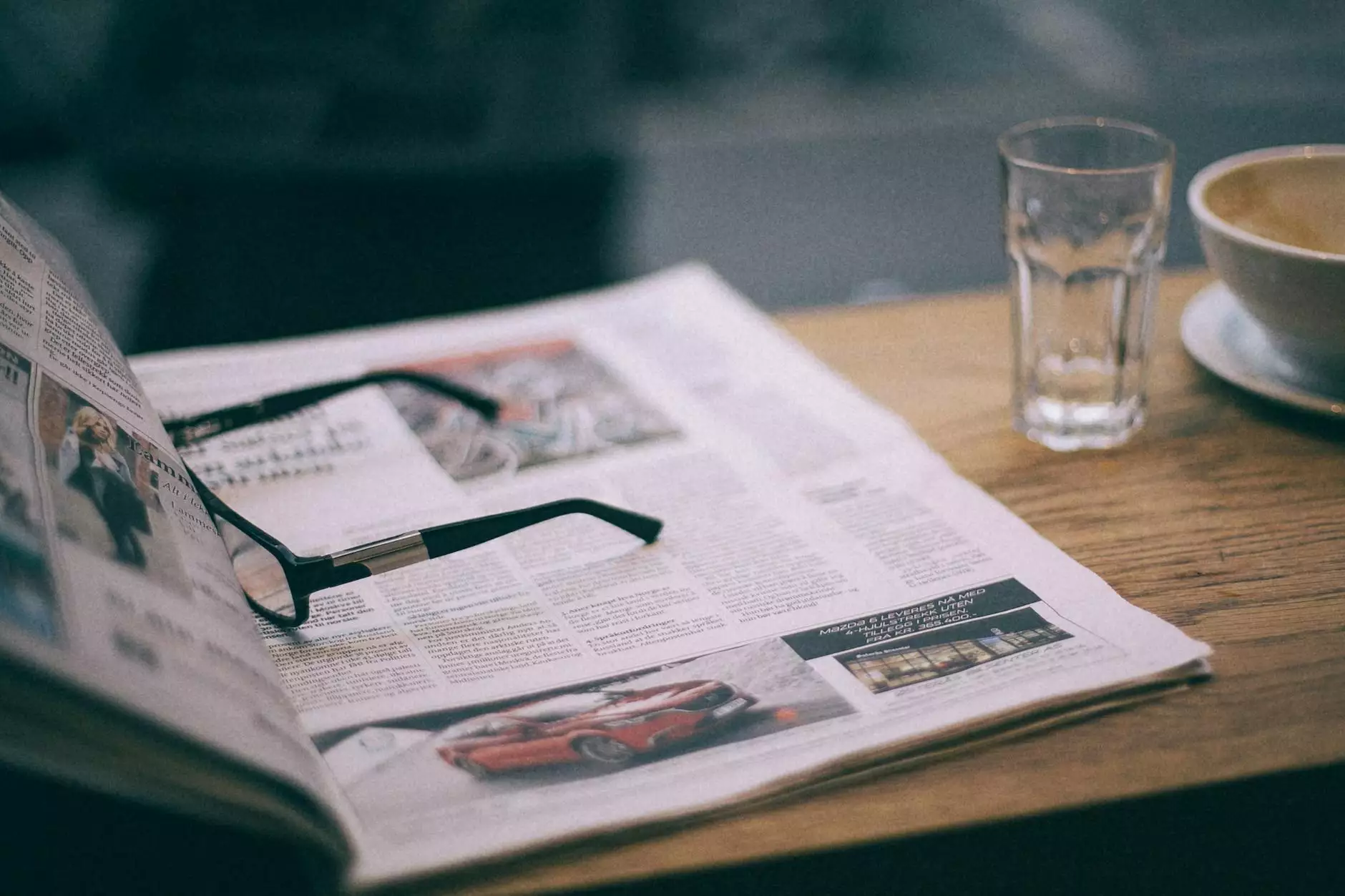
In today's fast-paced world, the ability to materialise ideas and concepts into tangible products is paramount for businesses looking to innovate and stay competitive. This is particularly true in the realm of 3D printing, a technology that has revolutionised countless industries by enabling the rapid prototyping and manufacturing of complex designs. At Infotron, we understand the importance of transforming visions into reality, and we aim to lead by example in this exciting field.
What Does It Mean to Materialise?
The term "materialise" refers to the act of making something tangible or real. In the context of business and technology, particularly 3D printing, it signifies the process of transforming abstract ideas into physical objects. This transformative capability is essential for businesses that want to bring innovative products to market swiftly and efficiently.
The Role of 3D Printing in Materialisation
3D printing technology plays a critical role in the process of materialisation. With the ability to create intricate designs from digital models, 3D printing enables businesses to produce prototypes and final products rapidly. This technology allows for greater design flexibility, reduces production costs, and shortens lead times, making it an invaluable tool for modern businesses.
Benefits of 3D Printing for Materialisation
- Innovation Acceleration: 3D printing allows for faster prototyping, enabling companies to test and iterate on their designs swiftly.
- Cost-Effectiveness: By reducing material waste and utilizing on-demand manufacturing, businesses can significantly lower production costs.
- Customization: Businesses can easily adapt designs to meet specific customer needs, turning bespoke ideas into reality.
- Complex Geometries: 3D printing can create intricate designs that would be impossible or prohibitively expensive to manufacture using traditional methods.
- Supply Chain Efficiency: With 3D printing, companies can produce parts locally, reducing reliance on distant supply chains and minimizing delays.
The Process of Materialising Ideas through 3D Printing
The journey of materialising ideas through 3D printing can be broken down into several key steps:
1. Ideation
The first step involves brainstorming and refining your idea. This phase is crucial as it sets the foundation for the project. Gather inspiration, conduct market research, and identify areas where innovation is needed.
2. Design Development
Once the idea is solidified, the next step is to develop a 3D model. This can be done using various CAD (Computer-Aided Design) software. Here, attention to detail is essential as the design will dictate the success of the printing process.
3. Prototyping
After completing the design, it is time to print a prototype. This initial model allows you to assess the functionality and aesthetics of the design, making necessary adjustments before mass production.
4. Iteration
Based on the prototype's performance, you may need to revisit the design and make revisions. The iterative process is one of the greatest strengths of 3D printing, allowing for rapid modifications based on feedback.
5. Final Production
Once the design is finalized, the production phase begins. Whether it’s a small batch or larger quantities, 3D printing can efficiently meet the demand.
3D Printing Technologies That Help Materialise Ideas
There are several different 3D printing technologies that cater to various needs and materials. Here are some of the most commonly used:
Stereolithography (SLA)
SLA uses a light source to cure liquid resin into hardened plastic. It is known for its high precision and ability to create intricate details, making it ideal for applications that require a professional finish.
Fused Deposition Modeling (FDM)
FDM is one of the most prevalent methods of 3D printing, using thermoplastic filaments that are melted and extruded through a nozzle. This technology is user-friendly and cost-effective, perfect for prototyping and small-scale production.
Selective Laser Sintering (SLS)
SLS uses a laser to sinter powdered material, binding it together to create a solid structure. This method is excellent for producing durable and functional parts, especially in engineering applications.
Digital Light Processing (DLP)
DLP is similar to SLA but uses a digital light projector to cure the resin. This results in faster print times and high-quality finishes, making it suitable for decorative items and intricate designs.
Materialise: A Leader in 3D Printing Solutions
At the forefront of the 3D printing revolution is Materialise, an innovative company that is transforming how businesses think about design and production. With a focus on software solutions and 3D printing services, Materialise helps companies materialise their ideas effectively.
Why Choose Materialise?
- Expertise: With years of experience in the industry, Materialise possesses the know-how to guide you through every step of the 3D printing process.
- Comprehensive Solutions: Whether you need software for design or complete manufacturing services, Materialise offers end-to-end solutions that cover all aspects of 3D printing.
- Innovation: Constantly pushing the boundaries of what's possible in 3D printing, Materialise invests heavily in research and development.
- Quality Assurance: Rigorous quality control measures are in place to ensure that every printed part meets the highest standards.
- Customization: Materialise understands the need for tailored solutions and works closely with clients to develop products that meet their unique requirements.
Case Studies: Successful Materialisations
To illustrate the impact of 3D printing and how businesses have successfully materialised their ideas, consider the following case studies:
Case Study 1: Automotive Part Production
A prominent automotive manufacturer faced challenges in producing complex components that were both lightweight and durable. By partnering with Materialise, they were able to leverage SLS technology to create custom parts that met their performance criteria. The result was a significant reduction in production time and costs, while also improving the overall design flexibility.
Case Study 2: Medical Device Development
A startup in the medical field aimed to develop a unique prosthetic device. By employing 3D printing technology, they were able to quickly iterate their designs based on patient feedback. Materialise provided support in both software development and prototyping, enabling them to bring their product to market in record time while maintaining high standards of quality.
The Future of Materialisation in Business
The future of materialising ideas through 3D printing is promising. As technology continues to advance, we can expect even more innovative applications and materials, enhancing the ability of businesses to create bespoke solutions. From aerospace to healthcare, the implications of 3D printing are vast, and forward-thinking companies are already preparing to embrace its potential.
Conclusion: Start Materialising Your Ideas Today
In conclusion, the ability to materialise concepts into tangible products is more accessible than ever, thanks to advancements in 3D printing. Companies like Infotron allow businesses to leverage these technologies, paving the way for innovation and success. If you are looking to transform your ideas into reality, we invite you to contact us and discover how we can help you with your 3D printing needs.
Call to Action
Don’t let your ideas remain just concepts. Materialise them with cutting-edge 3D printing technology. Visit Infotron today and see how we can bring your visions to life!