Understanding the Role of Engine Crankshaft Manufacturers
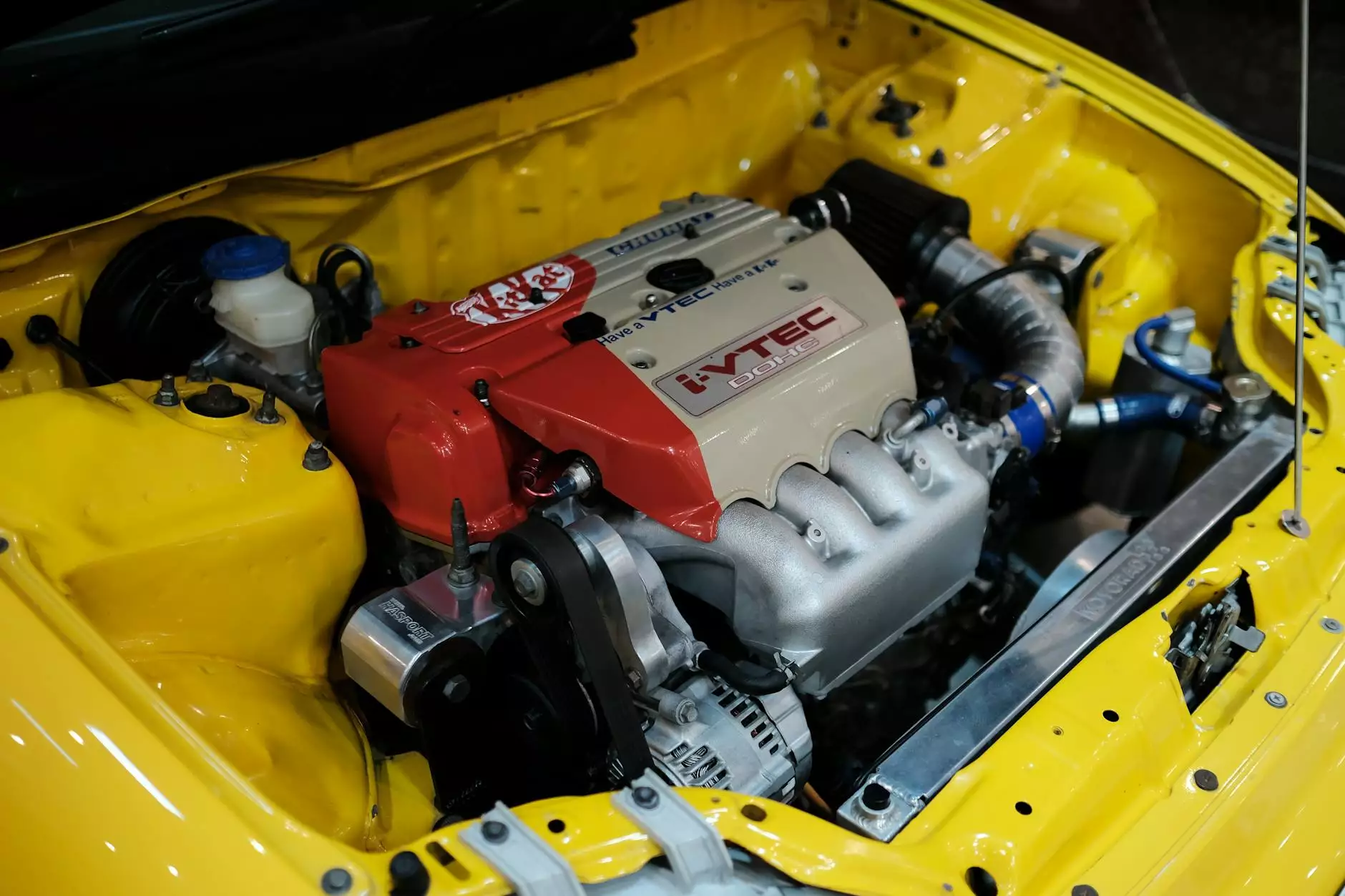
The engine crankshaft manufacturers play a crucial role in the automotive and machinery industries, particularly when it comes to diesel engines. A crankshaft is an essential component that converts the linear motion of pistons into rotational motion, which ultimately powers the vehicle. This article delves into the intricacies of crankshaft manufacturing, its significance in automotive mechanics, and why selecting the right manufacturer can significantly impact performance, reliability, and efficiency in diesel engines.
The Importance of Crankshafts in Diesel Engines
Diesel engines are renowned for their durability and fuel efficiency, making them a preferred choice for various applications, from heavy machinery to commercial vehicles. The crankshaft serves multiple vital functions:
- Power Transmission: Converts linear piston motion into rotational power.
- Balance: Helps maintain the engine's equilibrium by balancing the forces exerted by the reciprocating arms.
- Vibration Dampening: Reduces vibrations caused by the engine, promoting smoother operation.
Key Features of Quality Crankshafts
A crankshaft must meet several critical standards to ensure the efficient operation of an engine. Here are some characteristics to look for:
- Material Composition: High-quality crankshafts are typically made from alloy steel or cast iron, which provides robust strength and resilience.
- Precision Engineering: The manufacturing process should incorporate advanced technologies to achieve precise dimensions and tolerances, affecting fuel efficiency and performance.
- Surface Treatment: Processes like nitriding or hardening enhance durability and wear resistance.
The Manufacturing Process of Engine Crankshafts
Creating quality crankshafts involves several stages, from design to final inspection:
1. Design and Prototyping
Initially, engineers create detailed designs utilizing CAD software. Prototypes are made to test functionality and adjust designs as necessary.
2. Material Selection
The choice of materials is paramount. High-grade metals are selected for their strength and fatigue resistance, which are critical for lasting performance in demanding conditions.
3. Machining and Forging
After material selection, processes such as forging and machining shape the crankshaft. This step requires high precision to ensure all dimensions meet stringent specifications.
4. Heat Treatment
Heat treatment processes, including hardening and tempering, are employed to enhance the mechanical properties of the crankshaft, making it more resistant to wear and tear.
5. Finishing Touches
The crankshaft undergoes surface finishing processes, which may include grinding or polishing, to achieve the desired smoothness and reduce friction during operation.
6. Quality Control
Finally, each crankshaft is subjected to rigorous quality assessments. This includes dimensional checks, visual inspections, and often non-destructive testing methods to detect any underlying issues.
Leading Engine Crankshaft Manufacturers
The market hosts a variety of engine crankshaft manufacturers, each with unique strengths and product offerings. Here are some renowned manufacturers known for their quality and innovation:
- Mahindra Powerol - Known for high-performance and durable crankshafts tailored for industrial applications.
- Nissan Diesel - Renowned for manufacturing lightweight yet robust crankshafts for commercial trucks and buses.
- JCB - Their crankshafts offer superb balance and strength, essential for heavy-duty machinery.
- Client Diesel - A trusted source for diesel engine parts, including high-quality crankshafts, ensuring reliability and excellent performance.
Choosing the Right Manufacturer
When selecting a supplier for crankshafts, consider the following factors:
1. Experience and Expertise
Look for manufacturers with extensive experience in producing crankshafts. Their expertise often translates to higher quality products.
2. Quality Certifications
Reputable manufacturers should hold relevant quality certifications, ensuring compliance with industry standards. ISO certifications are particularly important.
3. Customer Reviews and Testimonials
Researching customer feedback can provide insights into the reliability and performance of the manufacturer's products.
4. Support Services
Consider manufacturers that offer strong after-sales support, including warranty services, technical assistance, and availability of replacement parts.
The Future of Crankshaft Manufacturing
The industry is evolving with technological advancements that enhance the manufacturing process:
1. Smart Manufacturing Techniques
Incorporating Industry 4.0 principles, manufacturers are adopting smart technologies to improve production efficiency and consistency.
2. Sustainability Initiatives
More manufacturers are focusing on sustainable practices, utilizing recycled materials, and minimizing waste during production.
3. Integration of Advanced Materials
The development of high-performance materials offers potential for lighter, stronger crankshafts that further enhance engine efficiency.
Conclusion
In conclusion, selecting quality engine crankshaft manufacturers is a vital component for ensuring the efficiency and durability of diesel engines. With the right manufacturer, such as client-diesel.com, you can ensure high-performance components that stand the test of time. As technology continues to evolve, staying informed about industry trends and choosing the right partners will ultimately lead to success in your operations.