Understanding the Importance of Plastic Injection Molding Manufacturers
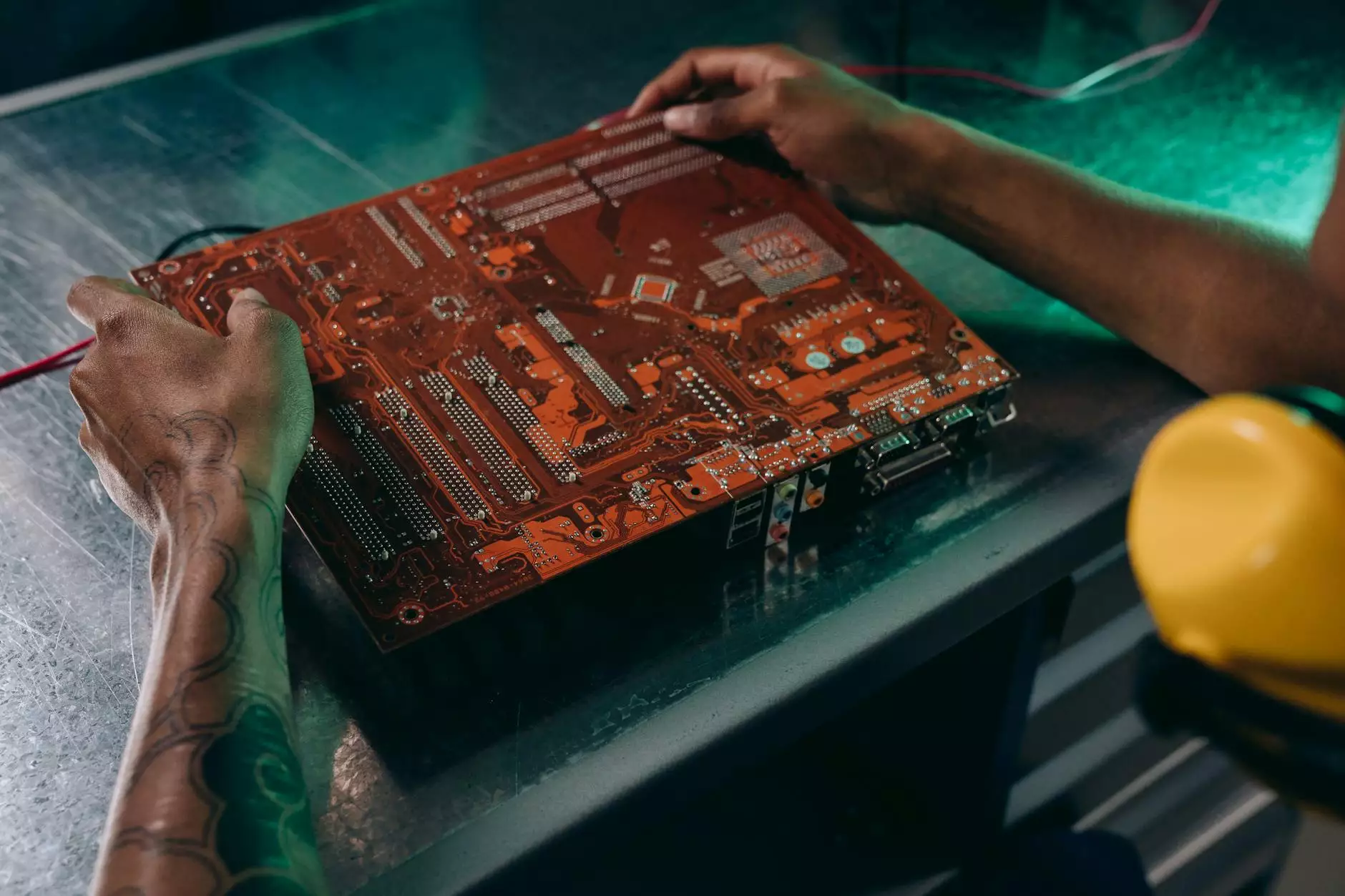
In the contemporary manufacturing landscape, plastic injection molding manufacturers play a crucial role in the production of intricate plastic parts that enable countless industries to function. This process not only provides enhanced efficiency and cost-effectiveness but also drives innovation in product design. In this comprehensive article, we delve deep into the myriad ways in which these manufacturers contribute to modern businesses, and why partnering with a reputable molding supplier can be a game-changer for your operations.
What is Plastic Injection Molding?
Plastic injection molding is a manufacturing process for producing parts by injecting molten material into a mold. It involves the following stages:
- Material Selection: The most common materials include thermoplastics and thermosetting plastics.
- Heating: The plastic granules are heated until they melt and transform into a viscous liquid.
- Injection: The molten plastic is injected into a pre-designed mold at high pressure.
- Cooling: The mold is cooled, allowing the plastic to harden and take shape.
- Demolding: The finished part is removed from the mold, completing the cycle.
The Role of Plastic Injection Molding Manufacturers
The significance of plastic injection molding manufacturers extends far beyond mere production. They are integral to various aspects of the manufacturing sector:
1. Innovative Product Design
Manufacturers utilize advanced technology to create intricate designs that were previously impossible with traditional manufacturing methods. This innovation leads to the creation of:
- Customized solutions: Tailored parts that meet specific client requirements.
- Complex geometries: Designs that enhance functionality and aesthetics.
- Prototyping capabilities: Rapid creation of prototypes for testing and evaluation.
2. Cost Efficiency
One of the most compelling advantages of working with plastic injection molding manufacturers is the cost efficiency gained through mass production. Here's how it benefits businesses:
- Reduced waste: The precision of the injection molding process minimizes material wastage.
- Economies of scale: Manufacturers can produce large quantities at a lower per-unit cost.
- Shortened production cycles: Faster production leads to quicker time-to-market, enhancing profitability.
3. Quality Assurance
Quality control is paramount in any manufacturing process. Top-notch plastic injection molding manufacturers implement rigorous quality assurance practices that include:
- Material inspections: Ensuring that raw materials meet strict standards.
- Process monitoring: Continuous monitoring during production to maintain consistency.
- Final testing: Comprehensive testing of finished products to ensure durability and functionality.
4. Sustainability
In recent years, sustainability has emerged as a pivotal concern for businesses globally. The plastic injection molding industry is adapting through:
- Recyclable materials: Utilizing plastics that can be recycled and reused.
- Energy-efficient processes: Implementing technologies that reduce energy consumption during production.
- Waste reduction initiatives: Adopting practices that minimize waste generated throughout the manufacturing lifecycle.
Choosing the Right Plastic Injection Molding Manufacturer
Partnering with the right manufacturer can make all the difference in your business operations. Here are key factors to consider when selecting plastic injection molding manufacturers:
1. Experience and Expertise
Look for manufacturers with a proven track record in the industry. Their experience can translate into better quality products and fewer production issues.
2. Technological Capability
Evaluate the technology they use for production. Advanced machinery and software can enhance precision and speed.
3. Customization Options
Discuss the extent to which they can customize projects according to your specific needs. Flexibility is crucial in today’s fast-paced market.
4. Customer Support
Strong customer support is vital for addressing any concerns during production. Be sure that the manufacturer values communication and responsiveness.
Case Studies: Success Stories of Plastic Injection Molding
To illustrate the impact of plastic injection molding manufacturers, let's explore a few success stories across various industries:
Case Study 1: Electronics Industry
A leading consumer electronics company needed high precision housing for their devices. By collaborating with a specialized plastic injection molding manufacturer, they achieved:
- Rapid prototyping: Allowing the company to test designs quickly.
- Cost savings: Reduced manufacturing costs with high-quality materials.
- Improved aesthetics: Enhanced surface finishes delivering a premium look.
Case Study 2: Automotive Sector
An automotive manufacturer faced challenges with the weight of traditional metal parts. By shifting to a skilled plastic injection molding manufacturer, they were able to:
- Reduce weight: Using advanced plastic composites that decreased overall vehicle weight.
- Enhance fuel efficiency: Resulting in lowered emissions and improved mileage.
- Increase customization: Allowing for tailored design features that improved user experience.
Case Study 3: Medical Devices
The medical industry requires high standards of hygiene and reliability. A medical device company worked with a trusted plastic injection molding manufacturer to ensure:
- Strict adherence to regulations: Complying with medical industry regulations with certified materials.
- High-quality assurance: Ensuring every piece met safety and efficacy standards.
- Speed to market: Rapid turnaround times enabling timely product launches.
The Future of Plastic Injection Molding
As we look ahead, the future of plastic injection molding manufacturers appears promising with several emerging trends:
1. Advancements in Material Science
Innovations in material science will lead to new, high-performance plastics that are lighter and more durable.
2. Automation and Smart Manufacturing
The integration of automation and IoT technology will enhance efficiency and productivity in the injection molding process.
3. Sustainable Practices
Sustainability will continue to be a focal point, with manufacturers adopting eco-friendly practices to meet consumer demands.
4. Globalization of Supply Chains
As manufacturers expand their operations globally, companies will have access to diverse resources and production capabilities, helping to tailor solutions for different markets.
Conclusion
In conclusion, the significance of plastic injection molding manufacturers cannot be overstated. They provide businesses with the ability to innovate, reduce costs, ensure quality, and adopt sustainable practices. As industries continue to evolve, selecting a reliable manufacturer will be pivotal in maintaining competitive advantage. For businesses looking to enhance their manufacturing process, examining the offerings of established companies such as DeepMould.net can be the first step towards achieving operational excellence.
By partnering with a reputable manufacturer, you’ll not only benefit from their technological expertise but also be positioned to meet the ever-changing demands of the market while driving your business forward into a sustainable future.