Understanding Silicone Membrane for Vacuum Forming
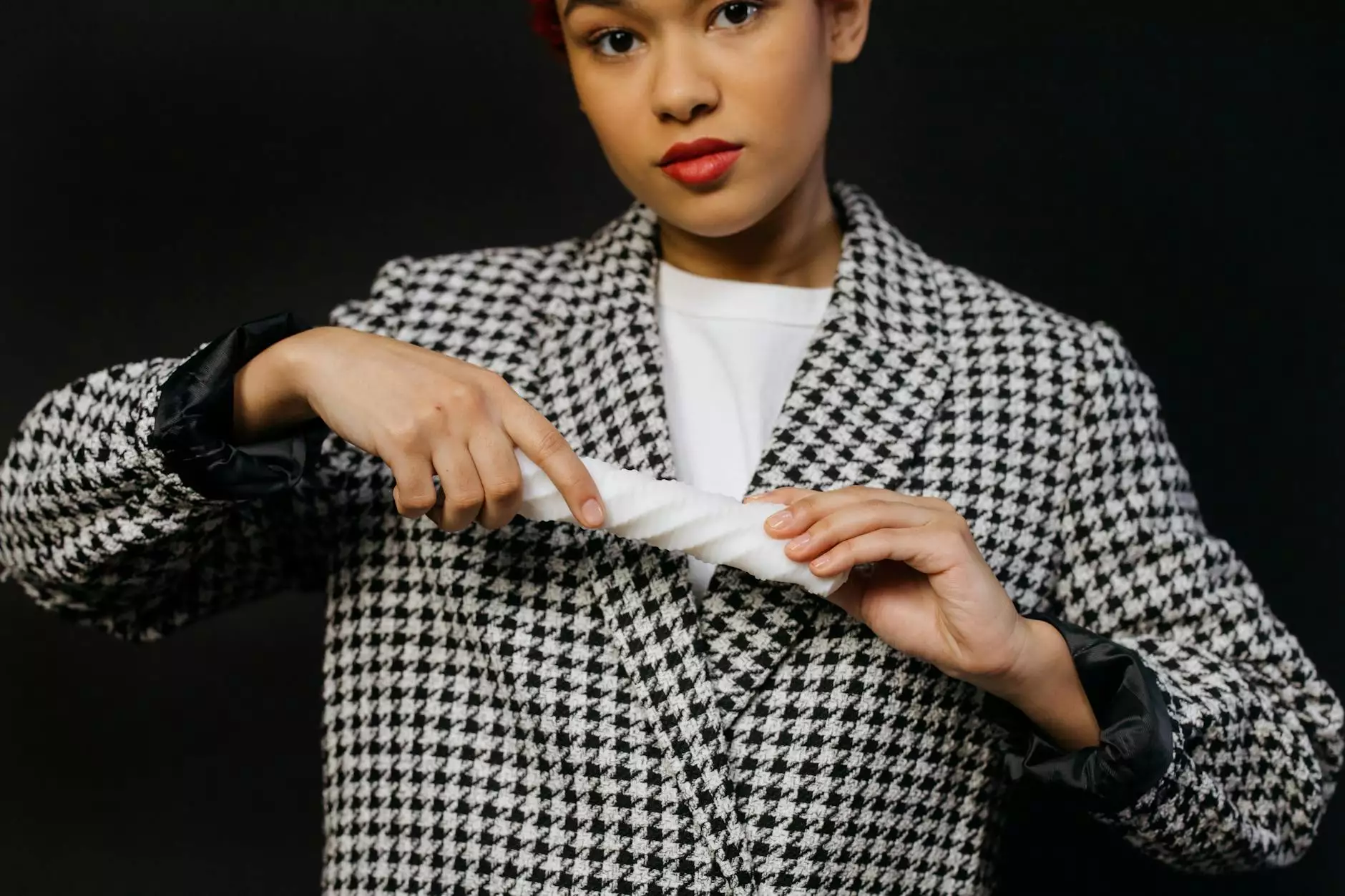
The silicone membrane for vacuum forming is a critical component in various manufacturing processes, particularly in the plastic, composite, and industrial design sectors. This article delves into the myriad benefits, applications, and specifications of silicone membranes, equipping businesses and professionals with the knowledge to optimize their production processes.
What is a Silicone Membrane?
A silicone membrane is a flexible material made from silicon-based polymers. These membranes are noted for their excellent thermal stability, resilience, and chemical resistance, making them an ideal choice for vacuum forming applications. These properties enable silicone membranes to withstand the stresses and strains of the forming process while maintaining their integrity and functionality.
Key Characteristics of Silicone Membranes
- High Flexibility: Silicone membranes exhibit excellent flexibility, allowing them to conform to complex shapes.
- Durable and Long-Lasting: They possess a longer lifespan compared to conventional rubber membranes, resulting in lower replacement costs.
- Temperature Resistance: Silicone can withstand extreme temperatures, making it suitable for heated vacuum forming processes.
- Chemical Resistance: Silicone membranes are resistant to many chemicals, preventing degradation during use.
Applications of Silicone Membranes in Vacuum Forming
The versatility of silicone membranes has led to widespread applications across numerous industries, including:
1. Automotive Manufacturing
The automotive industry uses silicone membranes for creating components such as dashboards, interior panels, and other intricate shapes that require precision.
2. Aerospace Engineering
In aerospace, silicone membranes enable the forming of lightweight and durable components essential for aircraft performance.
3. Packaging Solutions
Silicone membranes facilitate efficient vacuum forming used in packaging designs, ensuring products are well-protected during transit.
4. Consumer Goods Production
From toys to kitchenware, silicone membranes are fundamental in producing a range of consumer goods that require detailed and attractive design.
5. Medical Devices
The medical industry benefits from silicone membranes for creating various device components which must meet stringent regulatory requirements for safety and reliability.
Advantages of Using Silicone Membranes for Vacuum Forming
Choosing silicone membranes for vacuum forming over other materials provides several distinct advantages:
- Enhanced Product Quality: Silicone membranes contribute to a smoother surface finish in molded products, which can improve overall aesthetics and functionality.
- Cost Efficiency: Although the initial investment may be higher than for rubber membranes, the longevity and durability of silicone reduce overall costs in the long run.
- Customizability: Silicone membranes can be produced in various thicknesses and textures, tailored to meet specific production needs.
- Minimal Maintenance: Unlike some traditional materials, silicone requires minimal maintenance, allowing for higher productivity and efficiency.
Choosing the Right Silicone Membrane
When selecting a silicone membrane for vacuum forming, consider the following factors:
1. Material Specifications
Evaluate the technical specifications like hardness, thickness, and tensile strength to ensure compatibility with your manufacturing process.
2. Heat Resistance
Check the temperature range the silicone can withstand. This is crucial if the forming process involves heated molds.
3. Chemical Compatibility
Ensure that the silicone membrane can resist any chemicals it may encounter during production.
4. Cost and Availability
Compare prices and lead times from various suppliers to find a membrane that meets both your budget and timeline.
Maintenance of Silicone Membranes
To ensure a long lifespan for your silicone membranes, proper maintenance is essential:
- Regular Cleaning: Clean the membranes with mild detergents to remove any residues that may accumulate during use.
- Avoid Sharp Objects: Prevent damage by avoiding contact with sharp tools or abrasive surfaces.
- Storage Conditions: Store silicone membranes in a cool, dry place away from direct sunlight to prevent premature degradation.
Innovations in Silicone Membrane Technology
The field of silicone membranes continues to evolve, with innovations focused on improving performance, efficiency, and sustainability. Current research includes:
- Bio-Based Silicones: Development of materials derived from renewable resources to reduce environmental impact.
- Advanced Bonding Techniques: Enhancements in how membranes bond to substrates, resulting in stronger and more durable products.
- 3D Printing Integrations: Exploring the combination of silicone membranes with 3D printed structures for custom applications.
Conclusion
The silicone membrane for vacuum forming is an indispensable tool in modern manufacturing, offering numerous benefits that enhance product development across multiple sectors. With their remarkable versatility, durability, and efficacy, silicone membranes are leading the way in innovative production techniques. By understanding their advantages and proper usage, businesses can maximize efficiency, reduce cost, and streamline their operations.
For those looking to acquire high-quality silicone membranes, vacuum-presses.com provides a comprehensive selection, ensuring all your vacuum system parts and membrane needs are met with expertise and quality. By investing in top-tier silicone membranes, businesses can elevate their production processes to new heights.